第一篇:炼油厂顶岗实习报告
银 川 能 源 学 院
顶岗实习报告
题 目:炼油厂实习报告
实习单 位:中卫市盛大商贸有限公司
院 (系):中职部
专 业 :工业分析与检验
班 级 :1102
学 号 :1131130537
姓 名 :张 静
指 导 教 师 :王 颖
实习时间:2014年7月20日至2014年4月20日
目录
一 概述 ……3
二 装置概况及特点 ……4
1、装置概况……4
(1)装置原料……4
(2)装置产品……4
(3)装置规模……4
2、装置组成及设计范围……4
3、工艺技术特点……4
(1)原料过滤……4
(2)减压脱沥青……5
(3)加氢精制……5
(4)加氢裂化……5
三 生产流程简述 ……5
1、原料预处理系统……5
2、加氢反应系统……6
(1)加氢精制部分……6
(2)加氢裂化部分……6
3、高低压分离系统……6
4、压缩机系统……7
5、分馏系统……8
(1)精制分馏系统……8
(2)裂化分馏系统……9
6、辅助系统……10
(1)硫化剂……10
(2)注水……10
(3)污油……10
(4)火炬……10
四 心得体会 ……10
五 致谢 ……12
炼油厂实习报告
前言
人生有好多的第一次,第一次走路、第一次上学、第一次恋爱……而我们正在接受着第一次走出校门面向社会的考验。这是我第一次经历社会实践。对于一个中专生而言,敢于接受挑战是一种基本的素质。
在现今社会,就业问题就似乎总是围绕在我们的身边,成了说不完的话题。招聘会上的招聘中总写着“有经验者优先”,可还在校园里面的我们这班学子社会经验也会拥有多少呢?为了拓展自身的知识面,扩大与社会的接触面,增加个人在社会竞争中的经验,锻炼和提高自己的能力,以便在以后毕业后能真正走入社会,能够适应国内外的经济形势的变化,并能够在生活和工作中很好地处理各方面的问题,我来到了内蒙古庆华煤化有限公司,开始了我长达一年的社会实践。实践,就是把我们在学校所学的理论知识,运用到客观实际中去,使自己所学的理论知识有用武之地。只学不实践,那么所学的就等于零。理论应该与实践相结合。另一方面,实践可为以后找工作打基础。通过这段时间的实习,学到一些在学校里学不到的东西。因为环境的不同,接触的人与事不同,从中所学的东西自然就不一样了。要学会从实践中学习,从学习中实践。
我所在的车间是以煤焦油加氢生产石脑油和柴油的车间,在学校我的专业是工业分析与检验,在车间进行生产操作的过程中,与我在学校学到的知识是紧密相关的。本套装置是国内为数不多的一套装置,我很荣幸成为了本套装置的员工。就在我们刚来厂子的时候,我感觉对他们并不陌生。见证了原油,成品油,在这期间,我也学会了很多书本上没有的知识。首先,我们在厂子里学习了本套装置的流程,因为只有流程学通了才能更好的控制整套装置;而后,我们开始从外操学起,就是打通从这个塔到那个罐之间的流程;最后,我们学习了dcs系统控制,以前在学校我们也有接触,但是呢那毕竟是软件在工厂了如果那一步开错或者先后顺序颠倒都可能会引起事故,所以我们每一步都学的很认真而且也很小心。有些知识在实践中也得到了验证,所以说实践是检验真理的唯一的办法。
下面我就简介一下我们这套装置的一些具体情况:
一、概 述
内蒙古庆华集团有限公司煤焦油加氢项目10万吨/年煤焦油加氢装置以丰富的煤化工副产品资源为依托,原料利用该公司及周边地区所产的煤焦油、蒽油和装置驰放气提纯的氢气,加氢生产石油脑、柴油,充分体现了合理规划、优化布局、循环经济的发展思路。装置含原料预处理、加氢反应、高低压分离、产品分馏等单元。
二、装置概况及特点
1、装置概况
(1)装置原料
装置原料为高温煤焦油,是经过煤的高温干馏出得出炉煤气,出炉煤气经冷却,吸收,分离等办法处理得到煤焦油。
(2)装置产品
装置主要产品石脑油、柴油馏分,副产品为富含沥青质的重油。主要运涂;柴油机燃料,汽车燃料,沥青用于防腐绝缘材料和铺路及建筑材料等。
(3)装置规模
公称规模:10 万吨/年(以加氢精制反应进料为基准),操作弹性为70——110%,年开工为8000 小时。
2、装置组成及设计范围
装置设计范围为装置界区内的全部工程设计。本装置由原料预处理系统(100 单元) 、加氢反应系统(200 单元) 、高低压分离系统(300单元)、压缩机系统(400 单元) 、分馏系统(500 单元)和辅助系统(600 单元)组成。
原料预处理系统包括离心过滤和减压蒸馏脱沥青质。 加氢反应系统包括加氢精制和加氢裂化两部分。高低压分离系统包括加氢精制生成油的热高分、冷高分、热低分、冷低分,加氢裂化生成油的冷高分、冷低分,以及相应的换热、冷却和冷凝系统压缩机系统包括新氢压缩机、精制循环氢压缩机、裂化循环氢压缩机。辅助单元包括添加硫化剂和高压注水等系统。
3、工艺技术特点
(1)原料过滤
根据煤焦油含有大量粉粒杂质的特点,设置了超级离心机,首先进行固液及油水的三相分离, 过滤脱除100μm以上的颗粒, 再经篮式过滤器,滤除更细小的固体颗粒,避免换热系统堵塞。
(2)减压脱沥青
原料中含有较多的也能影响反应器运行周期的胶质成分,不能通过过滤手段除去。同过蒸馏方式,可以脱除这部分胶质物,并进一步洗涤除去粉粒杂质。为避免结焦,蒸馏在负压下进行。通过以上措施,可有效地防止反应器压降过早升高,保护了加氢催化剂,延长了催化剂的使用寿命。
(3)加氢精制
加氢精制反应主要目的是:1、烯烃饱和--将不饱和的烯烃加氢,变成饱和的烷烃;2、脱硫--将原料中的硫化物氢解,转化成烃和硫化氢;3、脱氮--将原料中的氮化合物氢解,转化成烃和氨;4、脱氧--将原料中的氧化合物氢解,转化成烃和水。
(4)加氢裂化
加氢裂化的目的是使得未转化油进一步裂化成轻组分,提高轻油收率。
三、生产流程简述
1、原料预处理系统
原料煤焦油由罐区进料泵送入离心过滤机(s-1101)进行三相分离。脱除的氨水进入氨水罐,经氨水泵(p-1107)送出装置。脱除固体颗粒后的煤焦油进入进料缓冲罐(v-1101) ,经过泵(p-1101)加压,换热器(e-1101)与减压塔中段循环油换热至 147℃,再经过进料过滤器(s-1102ab)过滤掉固体杂质后,与精制产物(e-1303、e-1301)换热升温至340℃,再经减压炉(f-1101)加热到 395℃后进入减压塔(t-1101)。减压塔顶气体经空冷器(a-1101a——d)和水冷器(e-1103)冷凝冷却至 45℃,进入减压塔回流罐(v-1102)。减压塔真空由减顶抽真空系统(pk-1101ab)提供。减压塔回流罐(v-1102)中液体由减压塔顶油泵(p-1102ab)加压。一部分作为回流,返回减压塔顶。另一部分与热沉降罐(v-1103)底部污水(e-1105ab)、减压塔中段循环油(e-1102)换热升温至 150℃后进入热沉降罐 (v-1103) , 脱水后的减压塔顶油送入加氢精制进料缓冲罐 (v-1201)。减压塔中段油由减压塔中部集油箱抽出,经减压塔中段油泵(p-1103ab)加压,一部分通过 e-1102、e-1101 换热降温至 178℃,作为中段循环油,打入减压塔第二段填料上方和集油箱下方,洗涤煤焦油中的粉渣和胶质;另一部分直接送入加氢精制进料缓冲罐(v-1201)。减压塔底重油含有大量的粉渣和胶质,不能送去加氢,由减压塔底重油泵(p-1104ab)加压,经 e-1104 产汽降温后,送至装置外沥青造粒设施造粒。p-1104ab 设有返塔旁路,提高减压塔釜的防结垢能力。 减压塔中段油在后续加氢系统不正常时,经冷却器(e-1106)冷却后去中间原料罐。减压塔中段油可在罐区与原料煤焦油调合,改善进预处理原料性质,保证装置正常运转。
2、加氢反应系统
(1)加氢精制部分
v-1201 中的加氢精制原料油由加氢精制进料泵 p-1201ab 加压后,与e-1304 来的精制热氢混合,经e-1302 与加氢精制反应产物换热升温至 245℃(初期),通过与加氢精制循环氢混合微调进精制反应器 r-1201a 入口温度,经三台加氢精制反应器 r-1201a——c,对原料脱硫、脱氮、脱氧和烯烃饱和。三台反应器的各床层入口温度通过由精制循环氢压缩机 k-1402 来的冷氢控制。r-1201a入口反应压力控制在16.8mpa。410℃(初期)高温的反应产物送往高低压分离系统。精制加热炉(f-1201)用于开工时加热加氢精制原料。
(2)加氢裂化部分
v-1202 中的加氢裂化原料油由加氢裂化进料泵(p-1202ab)加压后,与e-1308 来的裂化热氢混合,通过与加氢裂化循环氢混合微调进裂化反应器r-1202a入口温度,经 e-1307a——d与加氢裂化反应产物换热升温至385℃(初期),进入串联的两台加氢裂化反应器 r-1202ab。两台反应器的各床层入口温度通过由裂化循环氢压缩机k-1403 来的冷氢控制。r-1202a入口反应压力控制在 16.8mpa。402℃(初期)高温的反应产物送往高低压分离系统。裂化加热炉(f-1202)用于开工时加热加氢裂化原料。
3、高低压分离系统
加氢精制反应产物经过 e-1301、e-1302、e-1303,分别与减压塔进料(一次)、加氢精制反应进料(二次)和减压塔进料(三次)换热,降温至260℃,入精制热高分罐(v-1301)进行气液分离。精制热高分罐的液体,减压后排入精制热低分罐(v-1302)。精制热高分罐顶部气体经过e-1304、e-1305,分别与精制循环氢、精制冷低分油换热,再由精制产物空冷器a-1301ab和水冷器e-1306 冷却到 43℃,入精制冷高分罐(v-1303)再次进行气液分离。其间,为避免反应产生的铵盐堵塞空冷器,在空冷器入口前注入脱氧(或脱盐)水。精制热低分罐(v-1302)底部设汽提段和汽提蒸汽,脱除热低分油中的硫化氢,顶部为汽液分离空间。精制热低分罐的液体,减压后进入精制分馏塔(t-1502)。精制热低分顶部气体减压后进入精制稳定塔(t-1501)。精制冷高分罐(v-1303)的液体,减压后排入精制冷低分罐(v-1304),气体进精制循环氢压缩机入口的精制循环氢缓冲罐(v-1402)。精制冷低分罐(v-1304)的液体,经 e-1305 与精制热高分罐(v-1301)顶部气体换热升温至 180℃后进入精制稳定塔(t-1501)。精制冷低分罐底设有分水包,含有铵盐的污水排入污水管网。
加氢裂化反应产物经过 e-1307a——d、e-1308、e-1309,分别与裂化反应进料、裂化循环氢、裂化冷低分油换热,降温至 185℃,再由裂化产物空冷器 a-1302 和水冷器 e-1310 冷却到 43℃,入裂化冷高分罐(v-1305)进行气液分离。其间,为避免反应产生的铵盐堵塞空冷器,在空冷器入口前间断注入脱氧(或脱盐)水。裂化冷高分罐的液体,减压后排入裂化冷低分罐(v-1306),气体进裂化循环氢压缩机入口的裂化循环氢缓冲罐(v-1403)。裂化冷低分罐的液体经 e-1309 与裂化反应产物换热升温至180℃后进入裂化稳定塔(t-1504)。裂化冷低分罐底设有分水包,含有铵盐的污水排入污水管网。
为确保安全运行,精制热高分罐(v-1301)、精制冷高分罐(v-1303)、裂化冷高分罐(v-1305)都设有液位低低检测,并可以联锁停车。
4、压缩机系统
本系统有新氢压缩机(k-1401ab,一用一备)、精制循环氢压缩机(k-1402ab,一用一备)、裂化循环氢压缩机(k-1403ab,一用一备)共6 台压缩机。精制循环氢系统和裂化循环氢系统各自独立。 补充的新氢由 psa 氢气提纯装置来,进入新氢压缩机入口缓冲罐(v-1401),可通过氢气排入火炬,调节新氢压缩机入口缓冲罐压力,正常氢气不排火炬。新氢经过新氢压缩机三级压缩升压至 17.25mpa,并送入反应系统的循环氢管线。来自精制冷高分罐(v-1303)的精制循环氢气,进入精制循环氢压缩机入口缓冲罐 (v-1402) 沉降分离凝液后, 经精制循环氢压缩机 (k-1402ab)压缩升压至17.25mpa。压缩机出口气体分为三个部分:一部分至加氢精制空冷器入口,用于稳定压缩机的运行,保持压缩机出口压力稳定;一部分作为控制精制反应床层温度的冷氢,直接送往精制反应系统;另一部分则与补充的新氢混合,经e-1304 换热升温后,作为精制反应循环氢气与精制进料混合送至反应器。v-1402 出口管线设有流量控制的放空系统,用于反应副产的不凝性轻组分的去除,以保证精制循环氢浓度。该部分气体排入火炬。v-1402 的操作压力为本装置加氢精制系统的总的系统压力控制点,主要由补充氢供应系统控制。
来自裂化冷高分罐(v-1305)的裂化循环氢气,进入裂化循环氢压缩机入口缓冲罐 (v-1403) 沉降分离凝液后, 经裂化循环氢压缩机 (k-1403ab)压缩升压至17.25mpa。压缩机出口气体分为三个部分:一部分至加氢裂化空冷器入口,用于稳定压缩机的运行,保持压缩机出口压力稳定;一部分作为控制裂化反应床层温度的冷氢,直接送往裂化反应系统;另一部分则与补充的新氢混合,经e-1308 换热升温后,作为裂化反应循环氢气与裂化进料混合送至反应器。v-1403 出口管线设有流量控制的放空系统,用于反应副产的不凝性轻组分的去除,以保证裂化循环氢浓度。该部分气体排入火炬。v-1403 的操作压力为本装置加氢裂化系统的总的系统压力控制点,主要由补充氢供应系统控制。为确保安全运行,精制循环氢压缩机和裂化循环氢压缩机入口缓冲罐都设有超高液位检测,并可以联锁停车;循环氢压缩机入口缓冲罐都设有慢速和快速两套泄压系统,供紧急状态泄压或停车使用。压缩机系统各分液罐的凝液集中送回精制冷低分罐。
5、分馏系统
(1)精制分馏系统
来自高低压分离系统的精制热低分气、精制冷低分油送入精制稳定塔(t-1501),精制稳定塔顶气体通过水冷器 e-1501 冷凝冷却至40℃,进入精制稳定塔回流罐(v-1501)。精制稳定塔回流罐气体排入脱硫系统,液体则经精制稳定塔回流泵(p-1501ab)作为全回流送回精制稳定塔顶。脱除轻组分的精制稳定塔底部液体,通过e-1503 与精制分馏塔(t-1502)塔底油换热后送入精制分馏塔进一步分离。精制稳定塔底再沸器(e-1502)的热源为精制分馏塔底来的循环尾油,再沸器返塔温度约272℃。来自高低压分离系统的精制热低分油与精制稳定塔底油混合后送入精制分馏塔(t-1502),精制分馏顶气体经空冷器 a-1501ab 冷凝冷却至 70℃,进入精制分馏塔回流罐(v-1502)。精制分馏塔回流罐为常压操作,几乎没有气体排放。精制分馏塔回流罐液体经精制石脑油泵(p-1504ab)加压后,一部分作为回流送回精制分馏塔顶,一部分与裂化分馏塔顶油混合作为石脑油产品经e-1504 冷却后送出装置。精制分馏塔回流罐的水相由分水包排出。精制柴油馏分由精制分馏塔中段流出,在精制柴油汽提塔(t-1503)中经蒸汽汽提,最终由精制柴油泵(p-1503ab)抽出,与裂化分馏塔中段柴油混合后,经柴油空冷器(a-1503)冷却至 50℃,作为产品送出装置。 精制分馏塔底的尾油由精制尾油泵(p-1502ab)分两路送出:一路经 e-1502 换热实现综合能量利用,最后通过精制分馏塔再沸炉(f-1501)升温至 385℃返塔;另一路流量经 e-1503 与精制分馏塔进料换热,作为加氢裂化的原料送至裂化进料缓冲罐(v-1202)。
(2)裂化分馏系统
来自高低压分离系统的裂化冷低分油送入裂化稳定塔(t-1504),裂化稳定塔顶气体通过水冷器 e-1505 冷凝冷却至40℃,进入裂化稳定塔回流罐(v-1503)。裂化稳定塔回流罐气体排入脱硫系统,液体则经裂化稳定塔回流泵(p-1506ab)作为全回流送回裂化稳定塔顶。脱除轻组分的裂化稳定塔底部液体,通过 e-1506 与裂化分馏塔(t-1505)塔底油换热后送入裂化分馏塔进一步分离。裂化稳定塔底再沸器(e-1506)的热源为裂化分馏塔底来的循环尾油,再沸器返塔温度约263℃。裂化分馏顶气体经空冷器 a-1502 冷凝冷却至70℃, 进入裂化分馏塔回流罐(v-1504)。裂化分馏塔回流罐为常压操作,几乎没有气体排放。裂化分馏塔回流罐液体经裂化石脑油泵(p-1509ab)加压后,一部分作为回流送回裂化分馏塔顶,一部分与精制分馏塔顶油混合作为石脑油产品经e-1504 冷却后送出装置。裂化分馏塔回流罐的水相由分水包排出。裂化柴油馏分由裂化分馏塔中段流出,在裂化柴油汽提塔(t-1506)中经蒸汽汽提,最终由裂化柴油泵(p-1508ab)抽出,与精制分馏塔中段柴油混合后,经柴油空冷器(a-1503)冷却至50℃,作为产品送出装置。 裂化分馏塔底的尾油由裂化尾油泵(p-1507ab)分两路送出:一路经 e-1506 换热实现综合能量利用,最后通过裂化分馏塔再沸炉(f-1502)升温至385℃返塔;另一路流量经e-1507 与裂化分馏塔进料换热,作为加氢裂化的原料送至裂化进料缓冲罐(v-1202)。
6、辅助系统
(1)硫化剂
外购的硫化剂通过氮气吹扫卸入硫化剂罐v-1601 储存。催化剂开车硫化或运行期间补硫时,通过硫化剂泵 p-1601a 和 p-1601b 分别注入精制反应器 r-1201a/b/c 和裂化反应器 r-1202 a/b。正常运行期间补硫通过泵p-1601a/b 实现。
(2)注水
注水系统为加氢精制反应产物提供注水,注水位置在精制空冷器入口,以防止铵盐结晶堵塞设备。注水来源主要有两部分:一是回用 t-1502、t-1505 蒸汽汽提产生的含油废水;二是界外供应的脱氧水或除盐水。两种水可以混用,但回用水不应超过注水总量的一半。
(3)污油
全装置的轻污油管线接至装置内地下污油总管,最终排入污油罐v-1603。重污油通过重污油线进入 v-1603,v-1603 中的污油通过污油泵p-1603 间断送出装置。
(4)火炬
装置内各火炬排放点均接入火炬管网,火炬气总管接至放空管。放空罐内凝液视液位情况不定期地排入污油罐。放空罐气体出口总管接至装置外工厂火炬。
以上就是关于我们厂的一些情况。
四、心得体会
社会实践加深了我与社会各阶层人的感情,拉近了我与社会的距离,也让自己在社会实践中开拓了视野,增长了才干,进一步明确了我们青年学生的成材之路与肩负的历史使命。社会是学习和受教育的大课堂,在那片广阔的天地里,我们的人生价值得到了体现,为将来更加激烈的竞争打下了更为坚实的基础。我在实践中得到许多的感悟!
1、我知道了赚钱的不易。整天在工厂辛辛苦苦上班,天天面对的都是同一样事物,真的很无聊,很好辛苦。在那时,我才真正明白,原来父母挣钱真的很不容易。
2、在这次实践中,让我很有感触的一点就是人际交往方面,大家都知道社会上人际交往非常复杂,但是呢具体多么复杂,我想也很难说清楚,只有经历了才能了解。才能有深刻的感受。大家为了工作走到一起,每一个人都有自己的思想和个性,要跟他(她)们处理好关系得需要许多技巧,就看你怎样把握了。我想说的一点就是,在交际中,既然我们不能改变一些东西,那我们就学着适应它。如果还不行,那就改变一下适应它的办法。让我在这次社会实践中掌握了很多东西,最重要的就是使我在待人接物、怎样处理好人际关系这方面有了很大的进步。同时在这次实践中使我深深体会到我们必须在工作中勤于动手慢慢琢磨,不断学习不断积累。遇到不懂的地方,自己先想方设法解决,实在不行可以虚心请教他人,而没有自学能力的人迟早要被企业和社会所淘汰。
3、在公司里边,有很多的管理员,他们就如我们学校里边的领导和班级里面的班干部。要想成为一名好的管理,就必须要有好的管理办法,就要以艺术性的管理办法去管理好你的员工,你的下属,你班级里的同学们!要想让他们服从你的管理。那么你对每个员工或每个同学,要用到不同的管理办法,意思就是说:在管理时,要因人而异。
4、在工作上还要有自信。自信不是麻木的自夸,而是对自己的能力做出肯定。社会经验缺乏,学历不足等种种原因会使自己缺乏自信。其实有谁一生下来句啥都会的,只要有自信,就能克服心理障碍,那一切就变得容易解决了。
5、那就是化工厂的环境的确不怎样样,有人戏称:这里一年刮两次风,一次就刮半年。要想在这里呆下去,需要特别能吃苦才行,因此我学会了坚强。这是想要成功的人身上必须具有的。
一切认识都来源于实践。实践是认识的来源说明了亲身实践的必要性和重要性,但是呢并不排斥学习间接经验的必要性。实践的发展不断促进人类认识能力的发展。实践的不断发展,不断提出新的问题,促使人们去解决这些问题。而随着这些问题的不断解决,与此同步,人的认识能力也就不断地改善和提高!
致 谢
时间过的好快,转眼间,在庆华集团庆华煤化有限责任公司实习生活很快就要结束了,在这几个月的时间里,我学到了很多在学校学习不到的东西,真是令我受益匪浅,让我感觉很值得。这次实习不仅使我学到了课本上学不到的知识,更多的是我结识了一帮好朋友,在这里最值得我感谢的是我的师傅和事业部的各位领导们,是他们一直在指导我该怎样学习怎样操作应该注意哪些问题。在次我将永远铭记各位老师和领导的教诲。
实习生:张静
2014年4月
第二篇:南充炼油厂实习报告
实习报告 专业:
年级:
学 号 :
姓 名 :
带队教师 :
实习单位:四川石化南充炼油厂
时 间:
南充炼油厂简介:南充炼油化工总厂始建于1956年,1999年从四川石油管理局南充炼油厂分离重组而成的,隶属于国际上市公司——中国石油天然气股份有限公司西南油气田分公司。拥有常减压蒸馏、重油催化裂化、酮苯脱蜡(油)、异丙醇脱沥青等13套炼油装置以及配套辅助设施,目前原油加工能力为100万吨/年.拥有各种牌号品种一百多种。
实习目的:
生产实习是学生工程实践教育非常重要的环节,也是学生在进入工作单位之前接触现场设备、工艺等的一次全面性、系统性的学习机会。主要通过生产实习使学生增加对石化生产企业的了解, 掌握工艺流程、工艺设备、控制系统、生产管理,检修等方面的知识。增加对工艺流程、机器与设备在化工生产中的地位、使用情况、制造工艺及过程等方面的感性认识,为今后专业课学习打下良好基础。通过向工人及技术人员学习,了解社会和石化企业对大学生的基本要求实习内
实习内容:
进厂教育
安保人员为我们讲解南充石化炼油厂的发展史,在厂内应该注意的安全事项,及当今世界炼油厂的发展状况。
参观车间
一车间:常减压装置
1. 电脱盐 电脱盐是原油进入蒸馏前的一道预处理工序。从地底油层中开采出来的石油都伴有水和泥沙,水中溶解有无机盐,如nacl、mgcl2、cacl2等,这些物质的存在对加工过程危害很大,因此要通过电脱盐将其除去。由于无机盐大部分溶于水,故而脱盐与脱水同时进行。为脱除悬浮在原油中的盐粒,在原油中注入一定量的新鲜淡水(注入量一般为5%),ph值一般为5.5-6.5左右,呈弱碱性,这样有助于对乳化剂中乳化膜的破除和无机盐的脱除。在破乳剂和强电压的作用下,破坏了乳化液的保护膜,使水滴由小变大,不断聚合形成较大的水滴,借助于重力与电场的作用沉降下来与油分离
主要设备
1、混合设施。 油、水、破乳剂进脱盐罐前应充分混合,使水和破乳剂在原油中尽量分散到合适的浓度。一般来说,分散细,脱盐率高;但分散过细时可形成稳定乳化液反而使脱盐率下降。脱盐设备多用静态混合器与可调差压的混合阀串联来达到上述目的。
2、防爆高阻抗变压器 变压器是电脱盐设备的关键设备。
3、电脱盐罐 其主要部件为原油分配器与电级板。原油分配器的作用是使从底部进入的原油通过分配器后能够均匀地垂直向上流动,目的一般采用低速槽型分配器。电极板一般有水平和垂直两种形式。交流电脱盐罐常采用水平电极板,交直流脱盐罐则采用垂直电极板。水平电极板往往为两至三层. 当原油经过三重电脱盐罐后,原油中水的含量降到3mg/l以下,再进入加热炉进行加热,将原有加热到一定温度后即可进入常压精馏装置进行初步分馏。
2.常减压蒸馏
常压蒸馏原理:
精馏也称分馏,它是在精馏塔内同时进行的液体多次部分汽化和汽体多次部分冷凝的过程。原油之所以能够利用分馏的办法进行分离,其根本原因在于原油内部的各组分的沸点不同。在原油加工过程中,把原油加热到360~370℃左右进入常压分馏塔,在汽化段进行部分汽化,其中汽油、煤油、轻柴油、重柴油这些较低沸点的馏分优先汽化成为气体,而蜡油、渣油仍为液体。
减压蒸馏原理:
液体沸腾必要条件是蒸汽压必须等于外界压力。 降低外界压力就相当于降低液体的沸点。压力愈小,沸点降的愈低。如果蒸馏过程的压力低于大气压以下进行,这种过程称为减压蒸馏
原油经过常减压装置后,其中的汽油,柴油,煤油馏分被分离出来,但是呢这些馏分所占比例很低,最高只有30%远远不能满足工业需求。原油中大部分渣油,胶质沥青质从塔底流出,如果不利用起来就造成极大浪费。炼油厂将渣油送入重油催化裂化催化重整装置进行催化裂化,得到汽油、柴油等,以达到将渣油利用起来提高产量的目的。
二车间:重油催化裂化催化重整装置
催化裂化
催化裂化是石油炼厂从重质油生产汽油的主要过程之一。所产汽油辛烷值高(马达法80左右),安定性好,裂化气含丙烯、丁烯、异构烃多。催化裂化是按碳正离子机理进行的,催化剂促进了裂化、异构化和芳构化反应,裂化产物比热裂化具有更高的经济价值,气体中c3和c4较多,异构物多;汽油中异构烃多,二烯烃极少,芳烃较多。其主要反应包括:①分解,使重质烃转变为轻质烃;②异构化;③氢转移;④芳构化;⑤缩合反应、生焦反应。异构化和芳构化使低辛烷值的直链烃转变为高辛烷值的异构烃和芳烃。
催化裂化工段有三个部分组成,即反应—再生系统、分馏系统、吸收—稳定系统。
1.反应—再生系统
本车间采用的是提升管流化催化系统。
反应是在提升管反应器中进行的,由于反应过程中吸收热量和器壁散热,反应器进口和出口的温度是不相同的,进口温度高于出口大约20~30°c
减压蜡油和减压渣油分别从催化原料油中间罐区和燃料油灌区用泵抽入装置,在管线与轻柴油换热,再经经过其他一系列循环油换热后与渣油混合进加热炉加热与回炼油油浆混合后进入提升管反应器的下部喷嘴。
提升管反应器的进料与来自再生器的再生催化剂接触并立即汽化、反应。反应器生成的反应油气进入沉降器先经旋风分离器除去大量催化剂后,进入塔201下部,反应后的待生催化剂经汽提段汽提后进行结焦再生。燃烧生成的延期经旋风分离器除去大量催化剂后,先经双动滑阀,后经降压孔板降压消声器排至大气中。
2. 分馏系统
分馏系统的作用是将反应-再生系统的产物进行初步分离,得到部分产品和半成品。
3. 吸收—稳定系统
吸收稳定系统的任务是利用吸收和精馏的办法将来自催化分馏塔顶油气分离器的富气及粗汽油分离成干气(≤c2)、液化气(c3、c4)和蒸汽压合格的稳定汽油。吸收解吸过程要求同时达到三个目的:通过吸收塔尽可能的吸收c3、c4组分;通过解吸塔尽量将c2解吸出去。
催化重整
催化重整(简称重整)是在催化剂和氢气存在下,将常压蒸馏所得的轻汽油转化成含芳烃较高的重整汽油的过程。如果以80~180℃馏分为原料,产品为高辛烷值汽油;如果以60~165℃馏分为原料油,产品主要是苯、甲苯、二甲苯等芳烃, 重整过程副产氢气,可作为炼油厂加氢操作的氢源。重整的反应条件是:反应温度为490~525℃,反应压力为1~2兆帕。重整的工艺过程可分为原料预处理和重整两部分。 化学反应
包括以下四种主要反应:①环烷烃脱氢;②烷烃脱氢环化;③异构化;④加氢裂化。反应①、②生成芳烃,同时产生氢气,反应是吸热的;反应③将烃分子结构重排,为一放热反应(热效应不大);反应④使大分子烷烃断裂成较轻的烷烃和低分子气体,会减少液体收率,并消耗氢,反应是放热的。除以上反应外,还有烯烃的饱和及生焦等反应,各类反应进行的程度取决于操作条件、原料性质以及所用催化剂的类型。
经过裂化后的原油产生的废弃物是生产润滑油的原料,南充炼油厂采用的是溶剂脱蜡的办法来生产润滑油。
三车间:溶剂脱蜡
溶剂脱蜡是石油产品精制的一种重要办法,将润滑油原料通过溶剂稀释和冷冻,使其中的蜡结晶析出,进而降低润滑油凝固点的过程。工业上将含蜡原油通过原油蒸馏所得到的润滑油馏分,经过溶剂精制、溶剂脱蜡和加氢精制(或白土精制),可制成润滑油(基础油)和石蜡;
工艺流程
丙酮-苯脱蜡装置溶剂包括结晶、过滤、溶剂回收、冷冻等部分。原料与溶剂在带刮刀的套管结晶器内先与滤液换冷,并加入部分溶剂,再经氨冷和溶剂稀释后进行过滤。过滤后的滤液和蜡液分别进行蒸发和汽提以回收溶剂。
所加混合溶剂的组成与溶剂比因原料性质(沸程、含蜡量和粘度等) 及脱蜡深度的不同而异,一般甲基乙基酮-甲苯溶剂中含甲基乙基酮40%~60%,溶剂比为 1~4:1。稀释溶剂分几次加入, 有利于形成良好的蜡结晶,减少脱蜡温差及提高脱蜡油产率。原料在套管结晶器中的冷却速度不宜过快,以免生成过多的细小蜡结晶,不利于过滤。
过滤是在转鼓式真空过滤机内进行的,按照原料含蜡量的多少,分别采用一段或两段过滤,从滤液和蜡液中回收溶剂,均采用多效蒸发及汽提,以降低能耗。此外,为减少溶剂损失和防爆,还设有惰性气体防护系统。
实习总结:
通过实习,让我对炼厂有了更加全面的了解,为日后的实际工作打下了基础,也对所学的书本知识有了更加实际,深入的理解,把书本上的知识积极的应用到实际生产当中去,学习到了不少实际生产知识。也认识到了书本上所学的知识和实际生产是有差距的。
同时我也认识到,随着社会和科技的发展,炼油厂逐渐向大型化,自动化发展。南充炼油厂建厂较早,炼油装置是比较落后的,污染比较严重,噪音也很大。而且建厂之初没考虑
到城市的发展速度如此的快,以至于厂区被城市包围,安全隐患越来越严重,亟需调整关停。南充炼油厂利用自身在某些产品上的技术优势,选新址建厂改革,发展自身优势产业;随着新能源的开发,南充炼油厂兴建生物柴油炼制厂,以替代传统能源,具有高瞻性,这正符合当今石化产业的发展方向。
第三篇:吉化炼油厂实习报告
吉化炼油厂实习报告
吉林化工学院
化工与材料工程学院
油气储运工程
(学号)(姓名)
前言
我于2014年3月21日开始参加了由学校组织的为期2周的工厂实习活动。实习地点为吉林石化公司炼油厂。整个实习过程有:一、安全知识教育;二、熟悉流程、生产工艺;三、参观现场。主要的实习车间为成品车间、原油车间、装洗车间,最后还在工人师傅的带领下参观了整个厂区。实习内容以生产工艺、生产设备和生产操作为主。这次的实习任务主要是在工人师傅、工程技术人员和老师的指导帮助下,通过自学、讨论、参观听报告、参观现场、草图绘制、总结等实习方式,具体做到以下内容:
1、了解工厂基建、生产和发展的全过程;产品种类、生产办法、产品质量和技术规格;原料、产品的性质、贮藏、运输以及产品用途等方面的概况。
2、了解各工段的生产办法、工艺流程;主要工艺条件和主要设备结构;各工段之间的相互联系和相互影响。
实习目的
生产实习是高等工科院校教学过程的一个综合性实践教学环节之一,是学生在校期间完成理论教学向专业基础课和专业课过渡的必要环节,是对学生学习期间所获得知识的综合考察,也是理论与实践相结合的具体应用。
生产实习的主要目的是通过深入生产实际,使学生获得感性的生产工艺知识,在生产实习过程中,学生在工厂技术人员、带队教师的指导下,从生产工艺、原理、仪器、设备、仪表、厂房构筑、设备布置、技术指标、经济效益等等各方面在不同程度上掌握和了解,初步建立工程概念,为今后的专业基础课和专业课的理论教学打下良好的基础。同时培养学生的工程实践能力,学习先进的生产技术和企业组织管理知识,培养分析和解决工程实际问题的初步能力。提高综合素质,完成在校期间的工程基本训练。
工厂概况
炼油厂前身吉林省石油化工厂,建厂初期隶属于吉林省管理,1970年开工建设,1980年建成投产。1978年划归吉林化学工业公司管理,更名为吉林化学工业公司炼油厂;1994年股份制改造,更名为吉林化学工业股份有限公司炼油厂;2014年11月,更名为吉林石化公司炼油厂。。
截止2014年末,炼油厂有员工2014人,其中管理人员227人,专业技术人员223人,操作及服务人员1562;机关设综合办公室、生产科、技术科、机动科、安全环保科、组织人事科、党群工作科等7个科室;下辖常减压一车间、常减压二车间、催化裂化车间、重油催化车间、柴油加氢车间、加氢裂化车间、联合芳烃车间、硫磺回收车间、延迟焦化车间、成品车间、原油车间、装洗车间、分析车间、仪表车间、电气车间、供排水车间、锅炉车间、综合车间等18个生产及辅助车间。
炼油厂厂区占地面积155.42公顷,原油加工能力700万吨/年,有380万吨/年和320万吨/年两套常减压装置、140万吨/年和70万吨/年两套重油催化裂化装置、25万吨/年气体分馏装置、40万吨/年联合芳烃装置、90万吨/年加氢裂化装置、120万吨/年柴油加氢装置、100万吨/年延迟焦化装置、90万吨/年汽油脱硫醇装置、30万吨/年液化气脱硫装置、10万
吨/年催化干气脱硫装置、7万吨/年加氢干气脱硫装置、60万吨/年酸性水汽提体装置、64万吨/年溶剂再生装置、7000吨/年硫磺回收等16套生产装置,以及锅炉、循环水场、污水处理场、原油和成品油罐区、装卸车等辅助设施。主要产品有汽油、柴油、液化石油气、丙烯、苯、甲苯、邻二甲苯、混苯、化工原料油、石油焦、硫磺等20多个品种。2014年,原油加工总量675万吨,商品总量650万吨。
目前,炼油厂正在实施汽柴油质量升级和ⅱ常减压装置改造项目,项目主要包括:ⅱ常减压装置600万吨/年改造、催化裂化装置140万吨/年采用mip技术改造、建设60万吨/年液化气脱硫及气分装置、新建120万吨/年催化汽油加氢脱硫及烃重组联合装置、160万吨/年柴油加氢精制装置和2万吨/年硫磺回收装置、以及进行贮运系统、公用工程配套系统的改造。项目建成后工厂原油加工量可达1000万吨/年,汽油产品质量全部达到国ⅲ标准
车间实习记录
原油车间:
原油车间是以原油储存为主要任务的车间,车间的主要岗位分别是:原油罐区、蜡油罐区、原油卸车站、驻寨、计量、调度、办公室等。现车间共有人员为162人。岗位班次的运转方式为两种;一种是四班三倒(原油罐区、蜡油罐区),另一种为运输班(卸车站、调度)。
装置特点
a. 车间大部分原油储罐为浮顶油罐,此种储罐最大限度地减小了原油蒸发损失。 b. 三个原油罐区与卸车站之间流程相连,可以实现最科学的原料平衡。
c. 原油卸车站拥有四个原油上卸鹤位和两个渣油上卸鹤位,可以最快速地处理原油、渣油“瞎子车”。
d. 渣油站台为装卸一体化站台,可以同时实现渣油装车与卸车。
储存原油种类及输送形式
储存原油主要分轻、重两种组分,按来源主要分为大庆原油、吉林油田原油、俄罗斯原油、扎赉诺尔原油。
? 按输送形式主要分为管输原油和铁路槽车原油。
? 俄油、大庆油两种原油性质的差异。
工艺原理
利用液体油品流动性能,通过不同的管路自压或用泵压进行卸车及输送油品入装置。 成品车间
成品系统于1976年开始长周期的投入使用。其主要操作是接收、储存、调合、转输半成品油和成品油,并按要求进行加温、脱水及计量。其最主要特点是罐区分散、战线长且储存介质易燃易爆。
? 目前的成品车间共设置五个罐区,即:汽油罐区、柴油罐区、液化气罐区、渣油罐区、芳烃成品罐区,总存储能力19万立。9个泵房,即:汽油泵房、汽油消防泵房、汽油加铅泵房、柴油泵房、柴油消防泵房、液化气泵房、液化气消防泵房、渣油泵房、芳烃成品泵房。共有储罐77台,其中储油罐64台(包括10台球罐),其他储罐13台,冷换设备9台,机泵61台,其中油品转输用泵44台,消防用泵10台,其它机泵7台,以及全部出入该5个
罐区的全部输油管线约35万多延长米。
汽油罐区1976年建成。目前的汽油罐区共有储罐17台,其中5000立储罐11台,2014立储罐2台,1000立储罐4台,总储存能力63000立,共有离心泵12台,其中加铅泵1台,消防泵3台,消防泡沫罐2座。总占地面积约为93100米2。
? 柴油罐区1976年建成。最初的柴油罐区共有储罐11台,目前的柴油罐区共有13台储罐,其中5000立储罐9台,10000立储罐2台,2014立的储罐2台,总储存能力69000立。油品转输泵7台,加降凝剂泵2台,消防水泵3台,消防泡沫罐1座。总占地面积约为54600m2。 ? 渣油罐区1976年建成,目前渣油共有储罐7台,其中5000立储罐3台,3000立储罐2台,2014立储罐2台,总储存能力25000立,共有油品转输用泵7台,其中离心泵5台,蒸汽往复泵2台,总占地面积约为21600米2。
? 液化气罐区1976年建成,后有扩建和改建,目前共有球罐13台,总储存能力7200立.其中1981年建成400立球罐三台,1986年建成400立球罐四台,1992年建成400立球罐一台,随着生产装置的扩建和改造,2014年增建两台1000立球罐, 2014年增建3台1000立球罐。共有油品转输用泵10台,消防用水泵4台,另设汽车装车鹤位19个,总占地面积约为58000m2。
芳烃罐区1995建成,为30万吨乙烯装置配套。1996年10月投用,共有储罐8台,其中3000立储罐6台,1000立储罐2台,总储存能力20140立,共有油品转输用泵10台,总占地面积约为8400m2。
油品储罐及其附件
炼油厂成品车间用于储存油品的设施为油罐,油罐共分三种类型,分别是立式拱顶罐、立式浮顶罐和球罐。汽油罐区、四苯罐区全部为浮顶罐,柴油罐区为部分浮顶罐和部分拱顶罐。渣油罐为拱顶罐,液化气罐区储存液态烃,全部为压力球罐
油品储存的注意事项
? 1、易燃性。燃烧的难易和石油产品的闪点,燃点和自燃点三个指标有密切关系。石油闪点是鉴定石油产品馏分组成和发生火灾危险程度的重要标准。油品越轻闪点越低,着火危险性越大,但轻质油自燃点比重质油自燃点高,加此轻质油不会自燃。对重油来说闪点虽高,但自燃低,着火危险性同样也较大,故罐区不应有油布等垃圾堆放,尤其是夏季,防止自燃起火。
? 2、易爆性。石油产品易挥发产生可燃蒸气,这些气体和空气混合达到一定浓度,一遇明火都有发生火灾、爆炸危险。爆炸的危险性取决于物质的爆炸浓度范围。
? 3、易挥发、易扩散、易流淌性。
? 4、易产生静电。石油及产品本身是绝缘体,当它流经管路进入容器或车辆运油过程中,都有产生静电的特性,为了防止静电引起火灾,在油品储运过程中,设备都应装有导电接地设施;装车要控制流速并防止油料喷溅、冲击,尽量减少静电发生。
装洗车间
? 装洗车间建于1970年,是我厂生产的最后一道工序,担负着我厂成品油出厂主要任务。目前车间共有三座装车站台,分别是汽油装车站台,柴油装车一站台,柴油装车二站台;一坐挑车站台,一座洗槽站台。
? 汽油装车站台于1986年3月建成投用,设有2台浸没式内液压柴油大鹤管,另设有2台浸没式外液压汽油油大鹤管,同采用爬车牵引,双侧轮换液下装车。(2014年新建一套膜法油气回收装置与其配套)
? 柴油装车站台于2014年9月建成投用,设有2台浸没式内液压轻油大鹤管,采用爬车牵引,双侧轮换液下装车。
? 汽油装车站台设计装车能力为130万吨/年。两坐柴油装车站台设计装车能力为300万吨/年。汽油装车二站台设计装车能力为130万吨/年,目前正在建设中。
洗槽站共有48个洗车鹤位,采用双侧洗车,可洗汽油、柴油槽车。
工艺原理
? 1、根据液体油品流动性能,通过不同的管路自压或泵压进行装车。
? 2、对含污油槽车进行清洗,将清洗后的污油抽至污油罐内,进而达到洗车目的。 实习心得
在这段短暂的实习时间里,我的收获和感想很多,我觉得这种形式的参观实习非常的有意义,因为这比坐在课堂里听讲来得更为实际、直观。通过实地参观,我了解了生产的工艺流程,对工业生产的各个环节和主要设备都有了一定认识,并对这个行业有了一定的了解。我感到自己真的是学到了很多与专业相关的知识,同时也提高了我在生产实践中认识、分析问题的能力。为日后的实际工作打下了基础。但同时,也意识到了自己知识是如此匮乏,所以在今后的日子里,我们要更加努力的学习专业知识,填补自己的空白
我们通过实习对炼化公司的生产技术了较详细的认识,在此我们不仅加深了对专业知识的认识,也使我们开阔了眼界,也更加让我们感到了学习的重要性。为进一步学好专业课,从事这方面的研制、设计等打下良好的基础。在这次生产实习过程中,不但对所学习的知识加深了了解,更加重要的是更正了我们的劳动观点和提高了我们的独立工作能力等。
总之,理论学习是基础,但实际工作与理论的阐述也是多么的不同,在工作的闲暇之间,在同一些工作多年的人员的交谈中,深知,在工作岗位上,有着良好的业务能力是基础能力,是那么的重要。虽然实习的时间很短,但对我来说,收获是很大的。我会更加珍惜我的学习,并用实习的心得时时激励自己!
第四篇:炼油厂常压蒸馏顶岗实习总结
永坪炼油厂常压蒸馏顶岗实习总结
(学生:例子 指导教师:朱玉高)
一、实习简介
姓 名专业班级
性 别联系电话
实习单位
情况单位名称
性质(国营、集体或民营)
实习车间(或实习点)名称
详细地址
负责人(联系人)姓名、电话
实习岗位
岗位任务(该实习岗位具体做啥呢)
岗位素质技能要求(自我感觉哪些能力素质在工作中很重要)
是否被本单位录用
(或意向就业)
录用后工资待遇(元)
谈一谈对实习的体会及合理化的建议(包括对化工化学系专业教学实施方面):
二、实习风采
三、实习单位及岗位详细简介
前一段时间我们去永坪炼油厂顶岗实习,感触良多。石油是我们国家的命脉,石油加工工业更是国民经济的基础工业之一,我们在工厂里看到了很多先进的石油炼制设备和石油加工办法,感觉到我们在学校学习到的知识还是非常有限,远远达不到工厂的要求,这就要求我们在学习上还要多吸收一些课本以外的知识,多去工厂参观和实习,这样我们毕业以后才能更好、更快地达到工厂的要求。
陕西延长石油(集团)有限责任公司永坪炼油厂位于延安市宝塔区以北七十公里处的延川县永坪镇。其前身是1907年创办的“延长石油官厂炼油房”。在历史上不仅开辟了中国陆上石油炼制工业的先河,而且还为中国革命的胜利做出过重要的贡献。
长期以来,永坪炼油厂始终坚持“科技兴厂”的办厂方针,狠抓炼油规模生产,不断提高科技含量,先后进行了数十项技术改造,使永坪炼油厂从一个小型炼油厂发展成为一个拥有400万吨/年常压蒸馏装置,170万吨/年同轴式全重油催化裂化装置,15万吨/年催化重整装置,20万吨/年柴油加氢-临氢降凝装置,以及配套的风、水、电、汽、储运、产品精制、消防等设施,主要生产“三延牌”90#、93#、95#车用无铅汽油、石脑油,- 20#、- 15#、- 10#、- 5#、0#、5#、10#轻柴油 、煤油,油漆工业用溶剂油、三线馏分油、常压重油、催化重油和液化石油气产品,固定资产达18.2亿元的现代化中型石油炼制企业,轻质油收率、单位利税、单位加工费、产销率等主要技术经济指标在全国同类炼油厂中名列前茅。
与之同时,永坪炼油厂的管理工作也发生了本性的变化。先后荣获企业档案管理国家二级单位,全国化工安全卫生先生单企业、全国设备管理先进单位、全国精神文明建设工作先进单位、国家质量检测合格产品、全国行业质量示范企业、全国行业质量服务诚信aaa级企业、中国产品质量放心、售后服务满意、诚信维权模范单位、陕西省先进企业 、陕西省质量效益型企业 、陕西省售后服务先进单位、陕西省质量服务双满意单位、陕西省诚信单位、陕西省安全生产经营先进单位 、陕西省 “ 九五 ” 技术改造先进企业、陕西省爱国主义教育基地、陕西省依法治理示范单位、陕西省无泄漏工厂、陕西省清洁文明工厂等市级以上荣誉称号一百多项。继1998年一举成为陕西省首家质量体系认证的石化企业后,2014年也在陕西石化行业中率先通过了质量、环境和职业健康安全三个管理体系认证。
此外,永坪炼油厂的产品质量也跻身于国内外先进行列。生产的0#轻柴油荣获全国第六届科技博览会银奖和中国石油天然气总公司优质产品称号;0#、10#、-10#轻柴油荣获陕西省优质产品称号;10#轻柴油荣获陕西省质量免检产品称号;0#、10#、-10#轻柴油荣获陕西省质量信得过产品称号;-5#轻柴油荣获陕西省第三届技术成果交易洽谈会金奖;其主导产品车用无铅汽油、轻柴油和液化石油气全部荣获陕西省名牌产品称号。
面对永坪炼油厂的腾飞,曾目睹企业发展的原石油部副部长焦力人同志高兴地将永坪炼油厂誉为“延安明珠”。2014年,焦力人同志故地重游,欣喜之余,挥毫题词“喜看今日永炼,明珠更璀璨”。
四、实习目的
通过此次顶岗实习使我们了解现代工厂、车间、岗位的三级安全制度和相应的各种安全措施和注意事项;了解实习单位的主、副原料和辅助原料的性质、规格、质量指标,了解主要产品或半成品的名称、质量要求;了解实习岗位所采用的生产办法、基本原理、工艺主流程;了解实习岗位的主要设备名称、型号、规格和作用;了解实习岗位的操作规程、控制指标和主要工艺影响因素等。
通过此次顶岗实习,培养和提高我们理论联系实际的能力及分析问题和解决问题的能力,为我们毕业后到化工企业打下良好的基础。通过此次顶岗实习,培养我们的爱岗敬业、吃苦耐劳的精神,感受企业文化,提高职业素养,形成职业能力,为顺利就业奠定了坚实的基础。
在这次生产实习过程中,不但对所学习的知识加深了了解,更加重要的是更正了我们的劳动观点和提高了我们的独立工作能力等。
五、实习过程及内容
实习期间,我在永坪炼油厂常压蒸馏ⅱ车间运行二班工作,该班组一共有六位师傅,班长一位,正岗一位,司塔一位,司泵一位,电脱盐一位,技术员一位。我们这组一共两个实习生,我们主要从事于在现场了解和熟悉这个车间的生产流程、各流程原理及仪器装置的功能,并对石油化工行业有所了解。
(一)实习任务
通过此次顶岗实习,培养和提高我们理论联系实际的能力及分析问题和解决问题的能力,具体内容如下:
1、学习工厂、车间、岗位的三级安全制度和相应的各种安全措施及注意事项;
2、学习装置采用的主、副原料和辅助材料的性质、规格、质量指标,了解装置的主要产品或半成品的名称、质量要求;
3、学习岗位所采用的生产办法、基本原理、工艺主流程;
4、实习岗位的主要设备名称、型号、规格及作用;
5、学习实习岗位的操作规程、控制指标和主要工艺影响因素等;
6、学习实习岗位设备的开停车步骤,操作要点及出现各种情况时的处理及解决措施;
7、学习掌握实习岗位的主要仪表控制点,仪表种类、结构、特点及作用;
8、学习实习岗位化工原料及产品的分析检测办法。
(二)实习基本要求:
1、学生在实习企业必须遵守企业的各种规章制度和相应的劳动纪律,不能无故请假和擅离岗位。有特殊情况需要请假或改变实习企业的必须征得实习企业和指导教师的同意。
2、学生在实习期间必须严格遵守岗位操作规程和安全管理制度,严防工作责任事故和人身安全事故的发生。
3、必须遵纪守法,模范遵守公民的社会公德,不得从事法律法规、厂纪厂规、校纪校规所不允许的各项活动。
4、努力工作,积极完成实习单位指定的工作任务,虚心学习,积极、诚恳地向工人师傅、工程技术人员及企业管理人员求教,刻苦钻研。
5、应多与指导教师联系交流,及时得到教师指导。
(三)实习内容
1、装置概况
永坪炼油厂扩建一套80×104t/a催化炼化(z最大处理能力为100×104t/a)其原料为常压常压重油,为了满足催化装置对原料的要求,需新建一套加工延长混合原油,生产规模为200×104 t/a常压蒸馏装置。
新建的200×104t/a常压蒸馏装置为新扩建催化炼化装置的配套工程,常压蒸馏装置与催化炼化装置,航煤精制装置等组成联合装置。200×104 t/a常压蒸馏装置主要由原油电脱盐部分与原油换热部分,初馏、常压蒸馏部分,燃料油系统,三注等部分组成。
常压蒸馏装置的主要产品有石脑油、航煤、溶剂油、柴油和常压重油。
2、设计原则
(1)采用先进、可靠的工艺技术和设备,是装置总体水平达到国内较好的水平。
(2)充分依托联合装置共用的设备,节约资源。
3、主要工艺方案
200×104 t/a常压蒸馏装置,采用初馏--常压蒸馏流程,初馏塔侧线,以减轻常压炉负荷及常压塔负荷。电脱盐部分采用交直流电脱盐技术,由于混合原油中盐含量较高,采用三级脱盐脱水,以满足脱后含盐≤3mg/l的要求。
4、常压蒸馏装置工艺流程简述
原油自罐区来经p101(原油泵)升压后均分两路。第一路原油依次经e101a、b(脱前原油-初顶油换热器),e104a、b(脱前原油-常一中油(ⅲ)换热器)和e405a-c(脱前原油-常底油(ⅳ)换热器)与热源换热。第二路原油依次经e102 a、b(脱前原油-常顶油气换热器)和e106 a、b(原油-常二线换热)与热源换热。上述两路原油合并后130℃进入v101a-c(原油电脱盐罐);经三级脱盐脱水后,脱后原油不分流,一路继续与热源换热。
脱后原油依次经e107 a、b(脱后原油-常底油(ⅲ)换热器),e108 a、b(脱后原油)依次经常底油换热器)e107 a、b(脱后原油-常一中(ⅱ)油换热器,e109a、b(脱后原油-常一线油换热器),e110(脱后原油-常二线(ⅲ)换热器),e111(脱后原油-常一中(ⅰ)换热器),e112(脱后原油-常三线(ⅱ)换热器),e113(脱后原油-常二线(ⅱ)换热器)和e114a-c(脱后原油-常底油(ⅱ)换热器)与热源换热到202℃进入t101(初馏塔)。
t101(初馏塔)顶经e101a、b,a101a、d(初顶油气空冷器)及e121(初顶油气冷却器)换热及冷凝冷却至40℃进入v102(初馏塔顶回流罐)进行油水分离。分离出的含油含s污水送往酸性水汽提装置;初顶油经p102a、b(初顶油泵)抽出后分为两部分,一部分返回塔顶作为回流;另一部分与常顶油一起去碱洗部分,而后送出装置。
初侧油经p103 a、b(初侧泵)抽出后送入常压塔。
初底油由p104 a、b(初底油泵)抽出经e115a、b(初底油-常三线油(ⅰ)换热器,e116(初底油-常二中换热器),e117 a、b(初底油(ⅰ)换热器)与热源换热到270℃后进f101(常压炉)加热到360℃进入t102(常压塔)。
t102(常压塔)塔顶油气经e102 a、b与原油换热后经a102 a-d(常顶油气空冷器)和e122(常顶油气冷凝器)冷凝冷却到40℃后进入v103(常顶产品及回流罐)进行气液分离。分离出的含油含s污水送往酸性水汽提装置;常顶油经p105a、b(常顶回流泵)抽出后分为两部分,一部分返回塔顶作为回流;另一部分和初顶油一起进行碱洗,而后送出装置。
常一线油从t102塔第10层或12层塔板自流进t103(常压汽提塔)上段,采用常二线油作为重沸器热源,常一线油气返回常压塔,重沸后的常一线油由p106 a、b(常一线油泵)抽出,经e109,a103(常一线油空冷器)和e123(常一线油冷却器)换热和冷却至40℃出装置。
常二线油从t102第24层或第26层塔板自流进入t103中段,采用0.3mpa过热蒸汽进行汽提,常二线油气返回常压塔,汽提后的常二线油由p108 a、b(常二线油泵)抽出,经e118(常一线重沸器),e113,e110,106 a、b 和a104 a、b(常二线油空冷器)换热和冷却至50℃出装置。
常三线油从t102第34层或第36层塔板自流进入t103下段,采用0.3mpa过热蒸汽进行汽提,常三线油气返回常压塔,汽提后的常三线油由p110 a、b(常三线油泵)抽出,经e115,e112,a105(常三线油空冷器)换热和冷却至70℃出装置。
常一中油由p107 a、b(常一中油泵)自t102第16层塔盘抽出,经e111、e108 a、b、e104 a、b换热后返回第14层塔盘上年。
常二中油由p109 a、b(常二中油泵)自t102第30层塔盘抽出,经e116换热后返回第28层塔盘上。
常压塔底油由p111 a、b(常底油泵)抽出,经e117 a、b,e114a-c,e107 a、b,和e105a-c换热至121℃进入催化。在常底油需要冷出料时常底油渣油经e124(常底油备用冷却器)冷却至90℃送至罐区。
5、塔设备的检修
(1)运行中检查:为确保塔设备的安全运行,必须做好日常检查,并记录检查结果,以作为定期停车检查、检修的历史资料。日常检查项目如下:
a.原料、成品及回流的回流量、温度、纯度、公用工程流体,如水蒸气、冷却水、压缩空气等的流量、温度及压力。
b.塔顶、塔底等出的压力及塔的压力降。
c.塔的温度。如果温度低于正常温度,应及时排水,并彻底排净。
d.安全装置、压力表、温度计、液面计等仪表是否正常,动作是否灵敏可靠。
e.保温保冷材料是否完整,并根据具体情况及时进行修复。
(2)停车检查:塔设备在一般情况下,每年定期检修1-2次,将设备打开,对其内部构件及壳体上大的损坏进行检查、检修。停车检查的主要项目如下:
a.检查塔盘水平度、支持件、连接件的腐蚀、松动等情况,必要时取出塔外进行清洗或更换。
b.检查塔底腐蚀、变形及各部位焊缝的情况,对塔壁、封头进料口处筒体、出入口连接等处进行超声波测原,判断设备的使用寿命。
c.全面检查安全阀、压力表、液面计有无发生堵塞现象,是否在规定的压力下动作,必要时重新进行调整和校验。·
d.如在运行中发现异常振动现象,停车检查时一定要查明原因,并妥善处理。
(3)塔体裂缝的修补
a.不穿透的裂缝:对深度不超过塔体壁厚40%的裂缝,应先在裂缝两端各钻一个孔,阻止裂缝继续延伸,再从裂缝两侧铲出坡口,深度以能铲掉裂缝为准,然后采用分段倒退法进行焊接,以减少焊应力和变形。
b.穿透的窄裂缝:对于宽度小于15mm的窄透裂缝,应先在裂缝两端各钻一个直径稍大于裂缝宽度的孔,并沿裂缝两侧铲出坡口;当厚度小于15mm时可采用单面坡口,厚度大于15mm时采用双面坡口。裂缝长度小于100mm时可一次性焊完,否则应采用分段倒退法进行焊接,以减少焊应力,施焊时,应从裂缝两端向中间焊接,并采用多层焊接。
c.穿透的宽裂缝:对于宽度大于15mm的穿透裂缝,应将带有整个裂缝的钢板切除,在切口边缘加工出口坡,在补焊上一块和被切除钢板尺寸和材料完全一样的钢板;被且催促的钢板不应小于250mm,长度比裂缝长度大50-100mm,以避免焊接补板的两条平行焊缝间彼此影响,焊接补板时应中板中心向两端对称分段焊接,以使补板四周间隙均匀,保证焊接质量。
6、操作事故处理
(1)冲塔(或满塔)
a.原因:原油含水大,仪表失灵塔底液面过高,侧线馏出过多,造成塔盘干板;汽提蒸汽带水引起突沸;仪表失灵进料量过大,气相线速大超负荷;进料温度突变,回流带水,回流量太少;原油性质变化大,轻组分含量过多。
b.现象:塔顶温度上升,其侧线温度上升显著;分馏效果变差,油品颜色变深,比重增大,馏分间重叠严重;塔顶及进料段压力上升;侧线产品不合格。
c.处理:将油品改进次品线(罐);强化电脱盐脱盐、脱水工作及回流罐脱水;降低或停止塔底通气;必须适可听风机以加大塔顶压力;严重时可降低炉温。
(2)原油带水
a.原因;原油罐存油少脱水不好;注水量过多或脱水不畅通;电脱盐罐变压器跳闸,不能充分沉降;原油乳化严重;谁界位过高或指示失真。
b.现象:换热系统升高,换热温度下降;闪蒸塔气相线速增大,塔压力增大;电脱盐罐跳闸;常压塔操作波动;侧线产品质量不合格;初馏塔进料温度下降;加热炉炉管压降增大;设备腐蚀加剧;常顶回流罐水界面过高;常压塔易形成雾沫夹带,影响产品馏出产量;严重带水时,塔底泵抽空,炉进料波动大,晃量,炉出口温度上升,炉膛温度急剧下降;同时使换热器憋压而泄露等。
c.处理:联系付倒罐或强化脱水工作,加大注破乳剂量,降低或停止注注水量;降低处理量稍降炉出口温度,关小或关闭塔底通气;产品改次品;调整操作,当原油含水量下降后再恢复正常。
(3)塔底泵抽空:
a.原因:塔底液面过低,或仪表指示失真;塔进料含水过多,泵体内产生气阻;塔底轻组分含量大,造成汽蚀;过热蒸汽温度低,带水;泵本身故障。
b.现象:泵出口压力表大幅度波动或回零;泵体产生异常声音;泵的出口压力下降,电机电流下降;塔底液面迅速上升。
c.处理:适当提高提高量,减少抽出量,提高塔底液面;原油含水大,切换原油罐,进一步稳定电脱盐操作;提高热蒸汽温度,塔上增加塔底通气量,减少轻组分含量;检查泵进口是否堵塞,个扫线蒸汽阀是否关严及进出口连通阀的关闭情况是否严实;切换备用泵,可适当降量,进一步查找原因;更换压力表。
(4)原油中断
a.原因:罐区油位过低或倒罐误操;原油管线破或堵塞;原油泵发生故障等。
b.处理:及时联系会炼进行处理;与调度,罐区等单位联系。改循环(闭)或停工处理;启动备用泵。
(四)实习过程
(1)安全教育 在实习开始时,学校组织我们到公司由专业人士对我们进行安全教育,讲解了安全问题的重要性和在实习中所要遇到的种种危险和潜在的危险等等。
(2)车间实习我们在车间实习是生产实习的主要方式。我们按照实习计划在指定的车间进行实习,通过观察、分析计算以及向车间工人和技术人员请教,圆满完成了规定的实习内容。
(3)理论与实际的结合 为了能够更加深入的进行车间实习,在实习过程中,我们结合了所学的书本知识与实习的要求,将理论与实际进行了完美的结合,也更加的促使我们不断地进行学习与研究。
(4)实习日记 在实习中,我们将每天的工作、观察研究的结果、收集的资料和图表、所听报告内容等均记入到了实习日记中。随时接受老师们的检查与批改。
六、实习感受
实习生活已经结束,但每次回忆起来,总是那么亲切,那么充实,那么难以忘怀。
在带队老师的悉心关照下,我们圆满完成了顶岗实习。技术员师傅的毫不保留的指导,使我们的实习生活非常充实,收获无数;同组同学积极的讨论,相互间的支持与配合,互相的体谅关心,让我的实习生活和业余生活都多了一些人性的关怀与温馨的感动。
实习虽然只有十周的时间,但是呢在带队老师的精心安排下,我们每人由一个师傅负责,跟师傅学习本岗位的相关知识。闲暇之际也轮串了其他车间,同时我们还有机会锻炼自己,自己做讲解员给其他组的同学们讲解自己所在的车间。我们在自己的车间中,通过请教技术员,自己研究,与同组同学讨论等方式,我对我自己所在的车间--常压蒸馏ⅱ车间有了深入的了解,同时也对《化工原理》、《石油加工工艺》、《化工工艺学》、《化工设备》、《化工腐蚀与防护》等课堂上所学的书本知识有了更加实际的理解,把书本上的知识积极的应用到实际生产当中去,学习到了不少实际生产知识。也认识到了书本上所学的知识和实际生产是有差距的。
十个周顶岗实习工作的磨练,培养了我良好的工作作风和埋头苦干的求实精神,树立了强烈的责任心,高度的责任感和团队精神。生产实践让我学会脱离浮躁和不切实际,心理上更加成熟坚定。为走向工作岗位做好充分准备,在今后的工作中,我将继承和发扬自己的优势,学习改进不足。适应企业发展要求,努力把自己的工作做的更好!
短短的十周时间,我学到了很多知识。在这里我要感谢我们学院的领导老师们的精心安排,感谢车间里的工程师技术员的耐心指导,感谢我同组的同学们的相互帮助。特别指出的是,感谢二位带队老师与我们同甘共苦,使我们对生活和学习都充满信心!
通过这次实习,让我对炼油厂有了更加全面的了解,为日后的实际工作打下了基础,同时使我更加热爱石油化工这个行业,在今后的日子里,我会更加努力的学习专业知识,为我国的石化事业贡献出自己的力量。
第五篇:茂名石化炼油厂实习报告
实习报告
实习时间:2014年10月10日—2014年10月23日
实习单位:中国石化茂名分公司炼油分部
实习地点:广东省茂名市
学院:化学与生态工程学院
班级:07化工班
姓名:马钰程
学号:107273050153
一、实习简述
2014年10月10日出发到化工厂认识实习,这次能有机会到中国石化茂名分公司炼油分部实习,我感到非常荣幸。虽然只有短短的两周的时间,但是呢在这段时间里,在带队老师和车间主任工程师的帮助和指导下,对于一些平常理论的东西,有了感性的认识,感觉受益匪浅。这对我们以后的学习和工作有很大的帮助,我在此感谢学院的领导和老师能给我们这样一次学习的机会,也感谢老师和各位主任工程师的悉心指导。.
二、实习工作说明:
我们这次实习,主要在中石化茂名炼油分部润滑油车间里进行实习。在糠醛、二蒸馏、轻质苯酮三个车间进行了为期两周的实习。在车间师傅的详细讲解和悉心指导下,我们详细的了解了每个工段的设备和操控系统,初步了解了工厂各个工段的工艺指标,对工厂的管理制度也进行了简单的了解。
三、实习单位简介、经营理念及发展历史:
茂名石化为国有特大型综合性石油化工企业,成立于 1955 年。经过 50 多年的发展,公司从生产人造石油开始到向加工天然原油转变,再到炼油化工一体化,现在已发展成为我国生产规模最大的石油化工生产企业。
1955 年 5 月 12 日,国务院批准成立茂名页岩油厂筹建处, 1958 年开始开采页岩油矿, 1958 年 3 月试产出页岩油。 1963 年, 100 万吨 / 年第一套常减压蒸馏装置建成投产,公司从生产人造油向以加工天然原油为主转变。 1964 年 5 月,公司更名为石油工业部茂名石油公司。经 60 年代和 70 年代初期的建设, 1974 年原油一次加工能力达到 500 万吨 / 年。 1975 年 5 月,公司更名为广东省茂名石油工业公司。 1976 年建成 15 万吨 / 年润滑油生产系统,炼油厂从燃料型向燃料 - 润滑油型转变。 1983 年,中国石油化工总公司成立,公司划归石化总公司管理, 1984 年 1 月,公司更名为中国石油化工总公司茂名石油工业公司。 1990 年以来, 250 万吨 / 年第三套常减压蒸馏、三催化、水东港成品油码头及我国大陆首座 25 万吨级单点系泊原油接卸储输系统相继建成投产,公司原油一次加工能力达到 850 万吨 / 年,二次加工能力达到 520 万吨 / 年,成为全国原油加工能力最大,加工进口原油数量最多,技术最先进的企业之一。 1991 年 3 月 12 日,国务院批准建设茂名 30 万吨 / 年乙烯工程。 1992 年 1 月,公司更名为中国石化茂名石油化工公司。 1993 年 11 月,茂名 30 万吨 / 年乙烯工程正式开工建设。 1996 年 8 月,茂名 30 万吨 / 年乙烯工程建成投产,公司实现了从以炼油为主向炼油化工一体化转变。为落实国务院五项优惠政策, 1999 年 5 月 12 日,以炼油厂、动力厂为基础,对主业经营部分资产进行改制重组,登记注册成立了茂名石化炼油化工股份有限公司。 1999 年,对炼油进行扩能改造,公司原油加工能力由 850 万吨 / 年扩大到
1350 万吨 / 年,成为我国首个炼油能力超千万吨的炼化企业。 2014 年以来,按照 “ 质量升级、隐患整改、结构调整、技术改造、挖潜增效 ” 的 “ 五位一体 ” 方针,公司新建了焦化、催化重整、柴油加氢等装置,并将原焦化装置进行改造,使炼油加工手段更为完备,装置结构进一步改善。 2014 年 12 月 15 日,实施 100 万吨 / 年乙烯改扩建工程, 2014 年 9 月 16 日 100 万吨 / 年乙烯改扩建工程建成投产,创造了国内乙烯工程规模最大、建设工期最短、投资成本最低、设备和技术国产化率最高的新纪录。至此,公司乙烯生产能力由 36 万吨 / 年扩大到 100 万吨 / 年,茂名石化成为我国首座 100 万吨 / 年乙烯生产基地。目前,茂名石化 2014 万吨 / 年 油品质量升级改扩建项目已列入国家石化产业调整和振兴规划,公司正朝着建设世界级生产规模的炼化企业目标迈进。茂名石化自成立以来多次受到上级部门的奖励和嘉奖,曾获全国企业管理最高荣誉 --" 金马奖 " 、全国五一劳动奖状、全国节能工作先进企业、全国思想政治工作优秀企业、全国精神文明建设先进单位、全国文明单位,公司党委获全国先进基层党组织,公司工会获全国“模范职工之家”等荣誉称号。 2014 年,公司获得建国 60 周年广东省功勋企业、全国十大国有企业典型荣誉称号。
四、实习过程简介
我们在茂石化的进厂实习时间为两周,前面三天为公司对我们进行安全教育及进厂前培训,在这三天里我学会了一个化工行业从业人员的基本安全条例;随后我们每个两天进一个车间学习。第一个两天我们到轻质酮苯脱蜡脱油车间进行学习,在这我们主要对车间的结晶系统、冷冻系统、真空过滤系统及回收系统进行了系统的学习。第二个两天我们则到糠醛装置车间进行学习,后面几天到二蒸馏车间进行学习。
五、实习感想
首先、毕业实习的顺利进行得益于扎实的专业知识。
用人单位在招聘员工的第一要看的就是你的专业技能是否过硬。我们一同过去的几位应聘者中有来自不同学校的同学,有一部分同学就是因为在专业知识的掌握上比别人逊色一点而落选。因为对于用人单位来说如果一个人有过硬的专业知识,他在这个特定的岗位上就会很快的得心应手,进而减少了用人单位要花很大的力气来培训一个员工。另外一好专业技术过硬的员工一定在学习上下过功夫,做事就可能比较真。这是后来我们经理在给我们几个通过面试的同学说。
第二、在工作中要有良好的学习能力,要有一套学习知识的系统,遇到问题自己能通过相关途径自行解决能力。
因为在工作中遇到问题各种各样,并不是每一种情况都能把握。在这个时候要想把工作做好一定要有良好的学习能力,通过不断的学习进而掌握相应技术,来解决工来中遇到的每一个问题。这样的学习能力,一方面来自向师傅们的学习,向工作经验丰富的人学习。另一方面就是自学的能力,在没有另人帮助的情况下自己也能通过努力,寻找相关途径来解决问题。
第三、良好的人际关系是我们顺利工作的保障。
在工作之中不只是同技术、同设备打交道,更重要的是同人的交往。所以一定要掌握好同事之间的交往原则和社交礼仪。这也是我们平时要注意的。我在这方面得益于在学校学生会的长期的锻炼,使我有一个比较和谐的人际关系,为顺利工作创造了良好的人际气氛。
另外在工作之中自己也有很多不足的地方。比如:缺乏实践经验,缺乏对相关行业的标准掌握等。所在我常提醒自己一定不要怕苦怕累,在掌握扎实的理论知识
的同时强化实践,做到理论联系实际。另一方面要不断的强化学习,学习新知识、新技术更好的为人民服务。
通过这次毕业实习,把自己在学校学习的到理论知识运用到社会的实践中去。一方面巩固所学知识,提高处理实际问题的能力。另一方面为顺利进行毕业设计做好准备,并为自己能顺利与社会接轨做好准备。毕业实习是我们从学校走向社会的一个过渡,它为我们顺利的走出校园,走向社会为国家、为人民更好服务做好了准备。
推荐站内搜索:日记大全300字、捉蚊趣事作文400字、二本大学排名及分数线、传记作文、成人高考、中小学教师考试网官网、陕西省教师资格证考试成绩查询、51专升本、小学五年级作文大全、童年读后感300字、
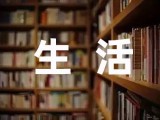